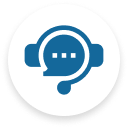
CONTACT US
Toshniwal Hyvac Pvt. Ltd.
Toshniwal Engineering & Systems Pvt. Ltd.
Toshniwal Infratech LLP.
#267, Kilpauk Garden Road, Chennai, Tamil Nadu - 600 010 (India)
©Toshniwal - All Rights Reserved
Toshniwal Hyvac Pvt. Ltd.
Toshniwal Engineering & Systems Pvt. Ltd.
Toshniwal Infratech LLP.
#267, Kilpauk Garden Road, Chennai, Tamil Nadu - 600 010 (India)
©Toshniwal - All Rights Reserved